Unsere Verfahren im Detail
Thermisches Spritzen
Thermisches Spritzen umfasst Verfahren, bei denen Spritzzustände inner- oder außerhalb von Spritzgeräten (an)geschmolzen werden um auf die Oberfläche von Werkstücken aufzuschleudern. Die Oberflächen werden dabei im Allgemeinen nicht angeschmolzen.
Schichtwerkstoffe in Form von:
- Pulver
- Draht
- Stab
Energiequelle:
- Flamme
- Lichtbogen
- Plasma
Produkt:
- Schicht
- Bauteil
Flammspritzen mit Draht
Ein Metalldraht von 1 bis 8 mm Durchmesser wird in die Spritzflamme geleitet. Dieser wird mittels Druckluft in fein verteilter Form auf die zu beschichtende Oberfläche geschleudert. Mit diesem Verfahren sind dicke Schichten möglich.
Flammspritzen mit Pulver (Foto)
Werkstoffe in Pulverform werden mittels Treibgas in einer Düse angeschmolzen und beschleunigt. Mit einer gashaltigen Flamme werden die Partikel aufgetragen. Dieses Verfahren wird für Verschleißschutz und Korrosionsschutz verwendet.
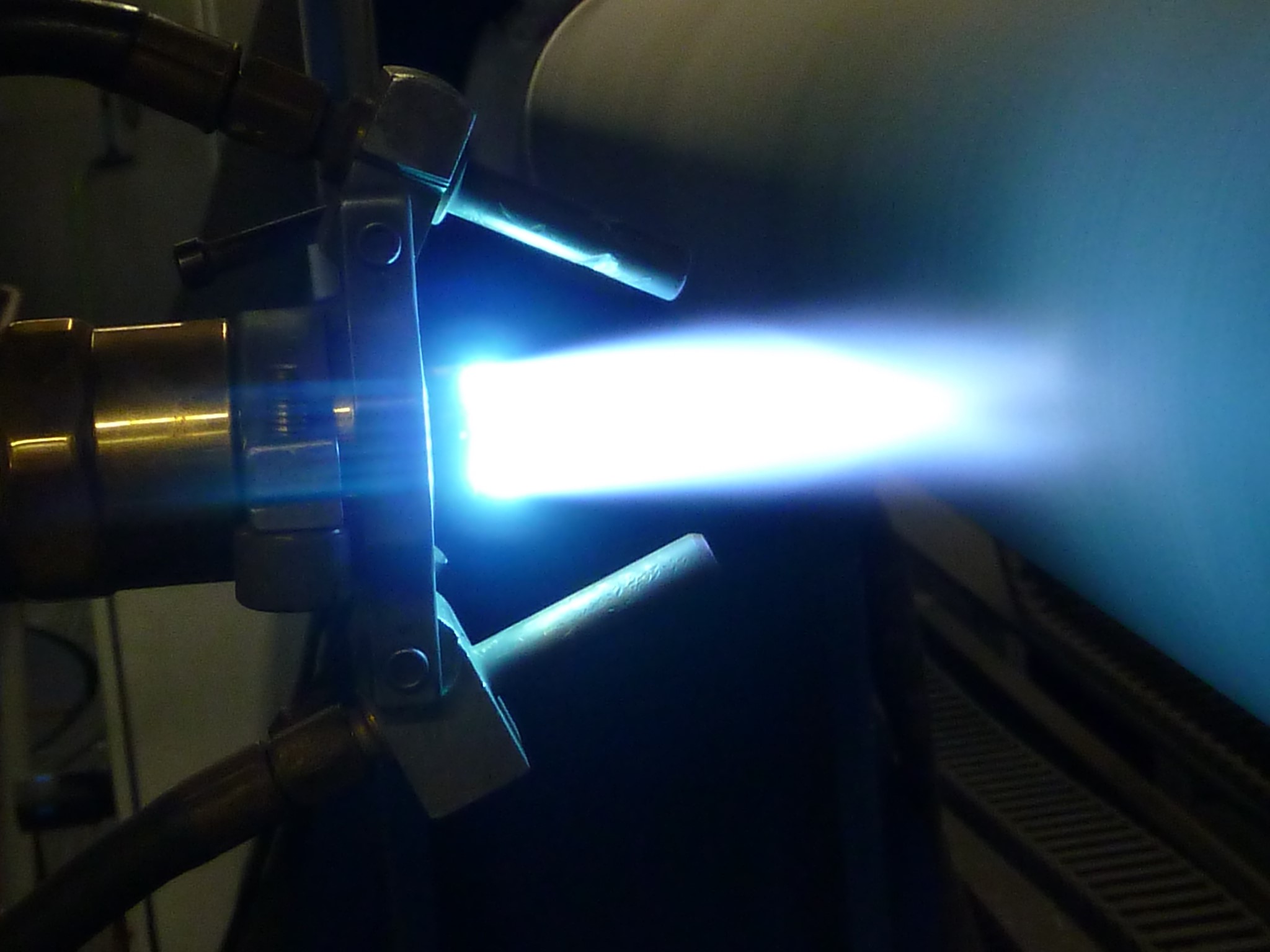
Lichtbogen
Zwei elektrisch leitende Drähte werden durch einen elektrisch erzeugten Lichtbogen angeschmolzen. Durch zugeführte Druckluft werden die Drähte zerstäubt und auf das zu spritzende Werkstück aufgetragen. Dieses Verfahren eignet sich besonders gut für großflächiges Beschichten.
Hochgeschwindigkeitsflammspritzen
(HVOF = High Velocity Oxygen Fuel)
Der HVOF Prozess wurde aus dem Pulverflammspritzen weiterentwickelt, als entdeckt wurde, dass eine höhere Geschwindigkeit der Partikel (bis achtfache Schallgeschwindigkeit) eine Verbesserung der Dichte, Kohäsion und Anhaftung der Schicht bewirkt.
Plasmabeschichten
Durch Ionisierung von Gasen (z.B. Argon) in einem elektrischen Lichtbogen wird ein Hochtemperatur-Plasmagasstrom (> 18.000 °C ) mit hoher Geschwindigkeit erzeugt. Pulverwerkstoffe werden angeschmolzen und mit hoher Geschwindigkeit auf das Werkstück aufgetragen. Durch die extrem hohen Temperaturen kann beinahe jedes Material, das sich verflüssigen lässt, schmelzen wenn man es in adäquater Pulvergröße zuführt. Das macht Plasmabeschichten zu dem vielfältigsten Beschichtungsverfahren.
RSW (Rotation Single Wire)
Dieses Verfahren wurde von FORD entwickelt. Es ist ein auf Draht basiertes, rotierendes Spritzverfahren, welches Lichtbogen- und Plasmaspritzen kombiniert. Der Drahtspritzwerkstoff wird über den elektrischen Lichtbogen aufgeschmolzen und mittels Druckluft zerstäubt und als Partikel in Richtung des Substrates beschleunigt. Beim Aufprall auf die vorbehandelte, aufgeraute Zylinderoberfläche entsteht ein lamellarer Schichtaufbau. Realisierte Durchmesser liegen zwischen 65 und 120 mm.
RSW dient zum Erzeugen von Zylinderlaufflächen in Aluminium-Motorblöcken im Großindustriellen Einsatz als auch im Reparaturbereich. Diese Laufflächen mussten bisher als Graugussliner aufwendig in die Geäuse eingepresst werden. Es könnten auch andere rotationssymmetrische Bauteile, wie Innenwandungen von Rohren, außerhalb des Automobilbereiches beschichtet werden.
Lasercladding
Ein Laserstrahl wird durch eine Faser zum Bearbeitungskopf geführt. Der Faser-Durchmesser und Auslegung der Optik bestimmen den Laserspot. Der Laserspot erzeugt ein Schmelzbad, in welches Pulver oder Draht zugeführt wird. Durch das Schmelzen der Oberfläche des Bauteils entsteht ein metallurgischer Verbund zum Substrat. Je nach Düse und Material ist die Pulverausnutzung bis zu 95 %.
Schichtwerkstoffe in Form von:
- Pulver
- Draht
Energiequelle:
- Laser
Produkt:
- Schicht
- Bauteil
Anwendungen:
- Auftragen von Verschleiß- & Korrosions-Schutzschichten
- Reparatur & Aufarbeitung von Bauteilen
- Herstellung neuer Oberflächengeometrien
- Innenschweißen von Bauteilen & Rohren ab 50 mm
- Veredeln & Aufarbeiten von Bauteilen
- Aufbauen von 3D Bauteilen
Vorhandene Anlagen
- HVOF Anlagen
- Lichtbogen Anlagen
- RSW Anlage
- Plasma Anlagen
- Flammspritz Anlagen (Draht und Pulver)
- Lasercladding Anlagen
Mechanische Bearbeitung
- Rundschleifmaschinen (CNC gesteuert) bis zu 4 m
- Flächenschleifmaschinen
- Drehbänke bis zu 4 m
- CNC Fräsmaschinen bis zu 1 m
Induktionshärten (Žilina, SK)
Die Induktionswärmebehandlung übernehmen wir in Form unserer Sonderhärteanlage in Lietava Lúčka (Žilina). Weiters bieten wir auch Laserhärten an. Wir arbeiten auch mit dem Serienhersteller von Präzisionsteilen Premat zusammen.
Anwendungen:
Induktionshärten eignet sich besonders zum Oberflächen-, Teil- aber auch Schüttguthärten, Anlassen von Funktionsoberflächen von Bauteilen wie:
- Drehflächen (Wellen, Stifte, Riemenscheiben, Zahnräder, Buchsen, Lagerringe)
- sphärische Oberflächen (Kugelgelenke)
- ebene Flächen (Führungsschienen) Technologie
Gegenwärtig haben wir Generatoren für die Hochfrequenz- und Mittelfrequenzheizung mit Auftragsmaschinen zum allmählichen Aushärten (max. Durchmesser 200 - 250 mm, max. Heizlänge - 2.000 mm) und zum einmaligen Aushärten. Diese Technologie ist prinzipiell für große Serien von Bauteilen geeignet, aber wir können auch einzelne Bauteile wärmebehandeln.

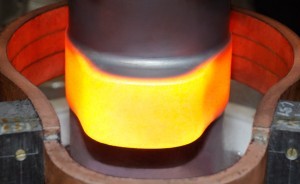