Our procedures in detail
Thermal spraying
Thermal spraying involves processes in which spray states are melted inside or outside spraying equipment to spin onto the surface of workpieces. The surfaces are generally not melted.
Coating materials in the form of:
- powder
- wire
- rod
Energy source:
- flame
- electric arc
- plasma
Product:
- coating
- component
Flame spraying with wire
A metal wire of 1 to 8 mm in diameter is directed into the spray flame, molten and accelerated by compressed air in the form of micrometer-size particles onto the surface to be coated. With this method thick coatings are possible.
Flame spraying with powder
Materials in powder form are molten by means of propellant gas into a nozzle and accelerated. The particles are applied with a gas-containing flame. This process is used for wear protection and corrosion protection.
Electric arc (picture)
Two electrically conductive wires are melted by an electric arc. Supplied compressed air, the wires are atomized and applied to the workpiece to be sprayed. This method is particularly suitable for large-area coating.
High velocity flame spraying
(HVOF = High Velocity Oxygen Fuel)
The HVOF process has evolved from powder flame spraying when it was discovered that higher particle velocity (eightfold sound velocity) improves the density, cohesion and adhesion of the layer.
Plasma coating
By ionizing gases (e.g., argon) in an electric arc, a high temperature plasma gas stream (> 18,000 °C) is generated at high speed. Powder materials are melted and applied to the workpiece at high speed. Due to the extremely high temperatures, almost any material that liquefies can be melted when fed in an adequate powder size. This makes plasma coating the most versatile coating procedure.
RSW (Rotation Single Wire)
This method was developed by FORD. It is a wire-based rotary injection process that combines arc and plasma spraying. The wire spraying material is melted by electric arc and atomized by compressed air and accelerated as particles in the direction of the substrate. The impact on the pretreated, roughened cylinder surface results in a lamellar layer structure. Implemented diameters are between 65 and 120 mm. RSW is used to create cylinder surfaces in aluminum engine blocks in large-scale industrial use as well as in the repair area. Previously, these running surfaces had to be pressed into the casings as gray cast-iron liners. It could also be other rotationally symmetric components, such as inner walls of pipes, outside the automotive area to be coated.
Laser cladding
A laser beam is guided through a fiber to the processing head. The fiber diameter and design of the optics determine the laser spot. The laser spot generates a molten pool into which powder or wire is fed. By melting the surface of the component a metallurgical composite is created to the substrate. Depending on the nozzle and material, powder utilization is up to 95%.
Coating materials:
- powder
- wire
Energy source::
- laser
Product:
- coating
- component
Applications:
- Application of wear and corrosion protection layers
- Repair & reconditioning of components
- Production of new surface geometries
- Internal welding of components and pipes from 50mm
- Refining and processing of components
- Building 3D components
Existing equipment
- HVOF plants
- arc plants
- RSW plants
- plasma systems
- flame spraying equipment (wire and powder)
- laser cladding facilities
Mechanical machining
- cylindrical grinding machines (CNC controlled) up to 4 m
- surface grinding machines
- lathes up to 4 m
- CNC milling machine up to 1 m
Induction hardening (Žilina, SK)
The induction heat treatment is provided by our special hardening plant in Lietava Lúčka (Žilina). Furthermore, we also offer laser hardening. We also cooperate with the series manufacturer of precision parts Premat.
Applications:
Induction hardening is particularly suitable for surface, partial as well as bulk hardening, tempering of functional surfaces of components such as:
- turning surfaces (shafts, pins, pulleys, gears, bushings, bearing rings)
- spherical surfaces (ball joints)
- flat surfaces (guide rails) technology
Currently we have generators for high frequency and medium frequency heating with grading machines (maximum diameter 200 - 250 mm, maximum heating length - 2,000 mm) and for single curing. This technology is suitable for large series of components, but can also be used to treat individual components.

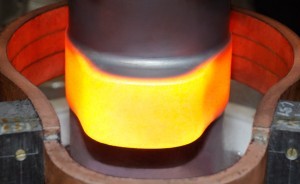